Смотрите как на ОАО «Речицадрев» делают фанеру
Источник: Dneprovec.by Фото: Ники КОТЛЯР
Фанерный завод – старейшее из речицких предприятий деревообработки. Именно с его основания в далеком 1904 году началась история этой отрасли в нашем городе. Теперь же это самое многочисленное структурное подразделение ОАО «Речицадрев», продукция которого пользуется неизменно высоким спросом у покупателей. 90% речицкой фанеры идет на экспорт, а это многое говорит о качестве товара и компетенциях коллектива фанерщиков. Мы проследили всю производственную цепочку: от бревна до готового листа фанеры, шаг за шагом.
1. Начало процесса
Все начинается с площадки выгрузки и сортировки сырья. Древесина самого высокого качества – фанерное сырье из березы и ольхи доставляется сюда вагонами или автотранспортом из лесхозов Гомельской и Витебской областей, а также с лесозаготовительного участка ОАО «Речицадрев». Продукция более низкого сорта – техсырье – отправляется на производство ДСП.
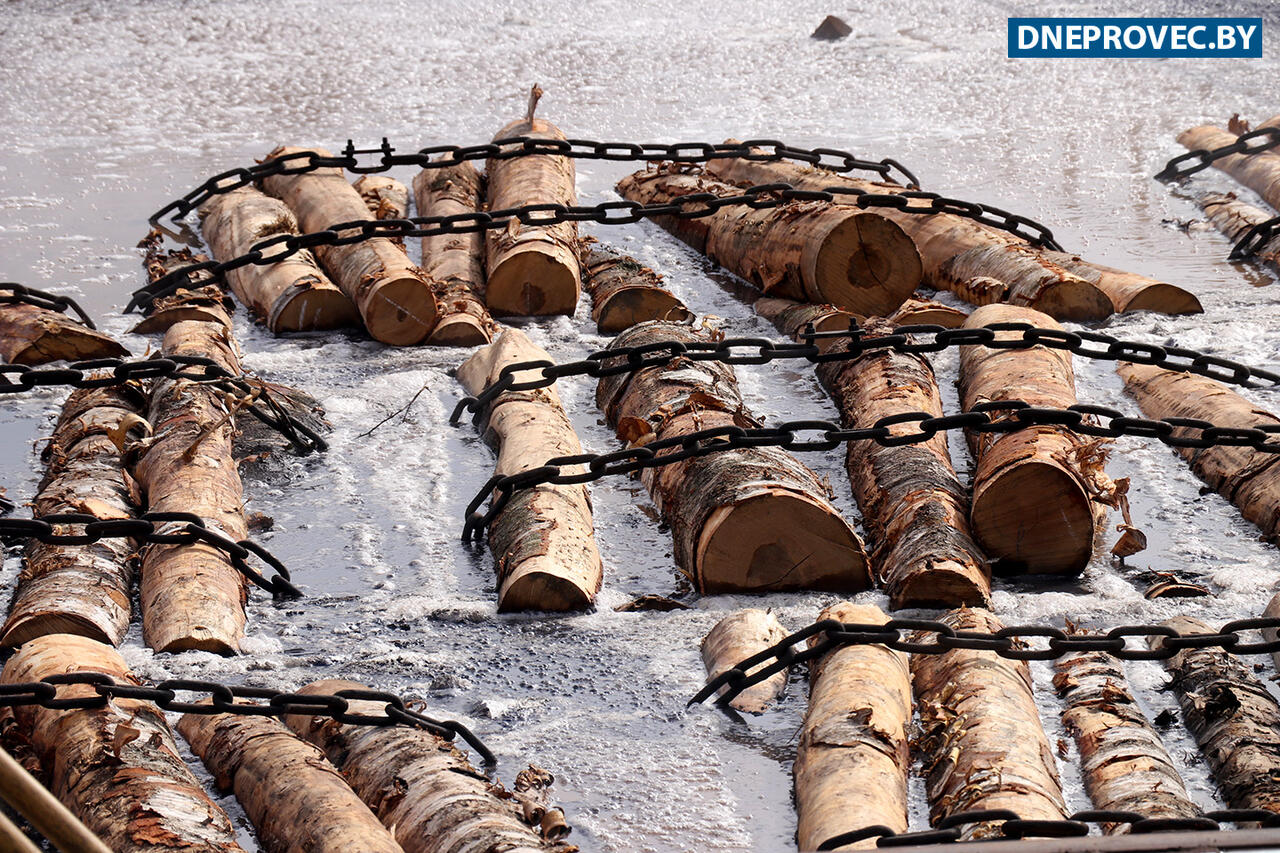
Отборные бревна поштучно распределяются по карманам-накопителям по 6 кубометров, где их связывают цепями, а потом козловой кран помещает такие связки в бассейны с горячей водой, в которых сырье находится около суток (срок зависит в том числе от толщины бревна), готовится к процессу лущения. Из бассейнов связка сырья отправляется на цепной транспортер, который по одному переправляет бревна в цех.
Бревна проходят через магнитную рамку, чтобы распознать металлические предметы, которые могли попасть в стволы деревьев. Такие элементы могут серьезно повредить оборудование. Опытные работники рассказывали, что таким образом находили осколки снарядов, пули, даже ордена Великой Отечественной войны.
2. Лущильный цех
По транспортеру бревно путешествует внутрь цеха, проходит через систему РАСТР, которая фиксирует главные параметры сырья: диаметр, длину, объем. Все это видно на мониторе у оператора.
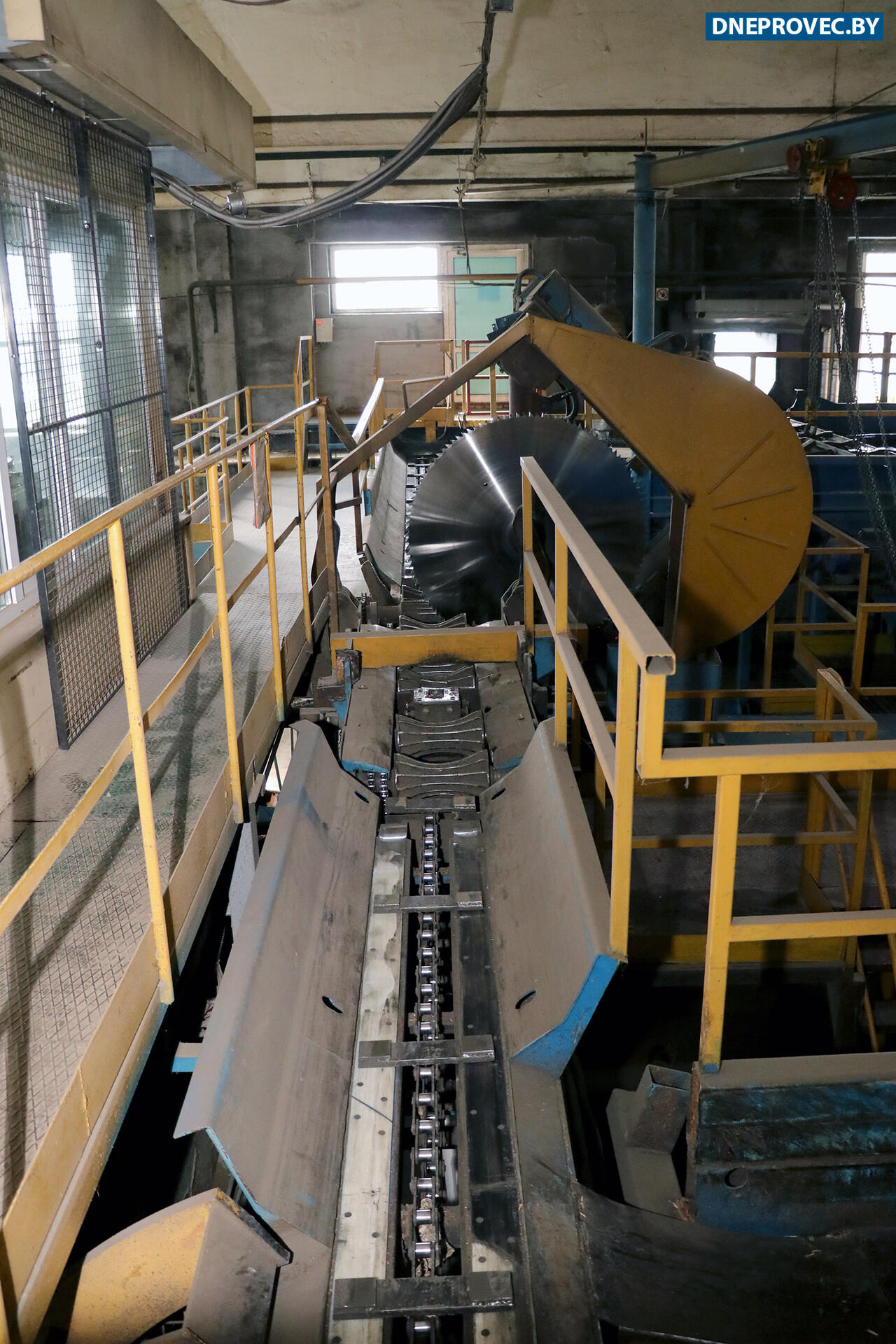
Раскряжовка – то есть подгонка под необходимые размеры – осуществляется с помощью огромных круглых пил. Расстояние от пилы до упора – ровно 1620 миллиметров, центровка осуществляется лазером. После этого заготовка отправляется на одну из трех лущильных линий (ОАО «Пролетарская свобода», город Ярославль, Россия). Работает еще одна линия – долущивания – финско-китайской фирмы RAUTE. Разница с российскими – в захвате бревна при помощи четырех роликов. Это позволяет справиться с более «сложным» сырьем.
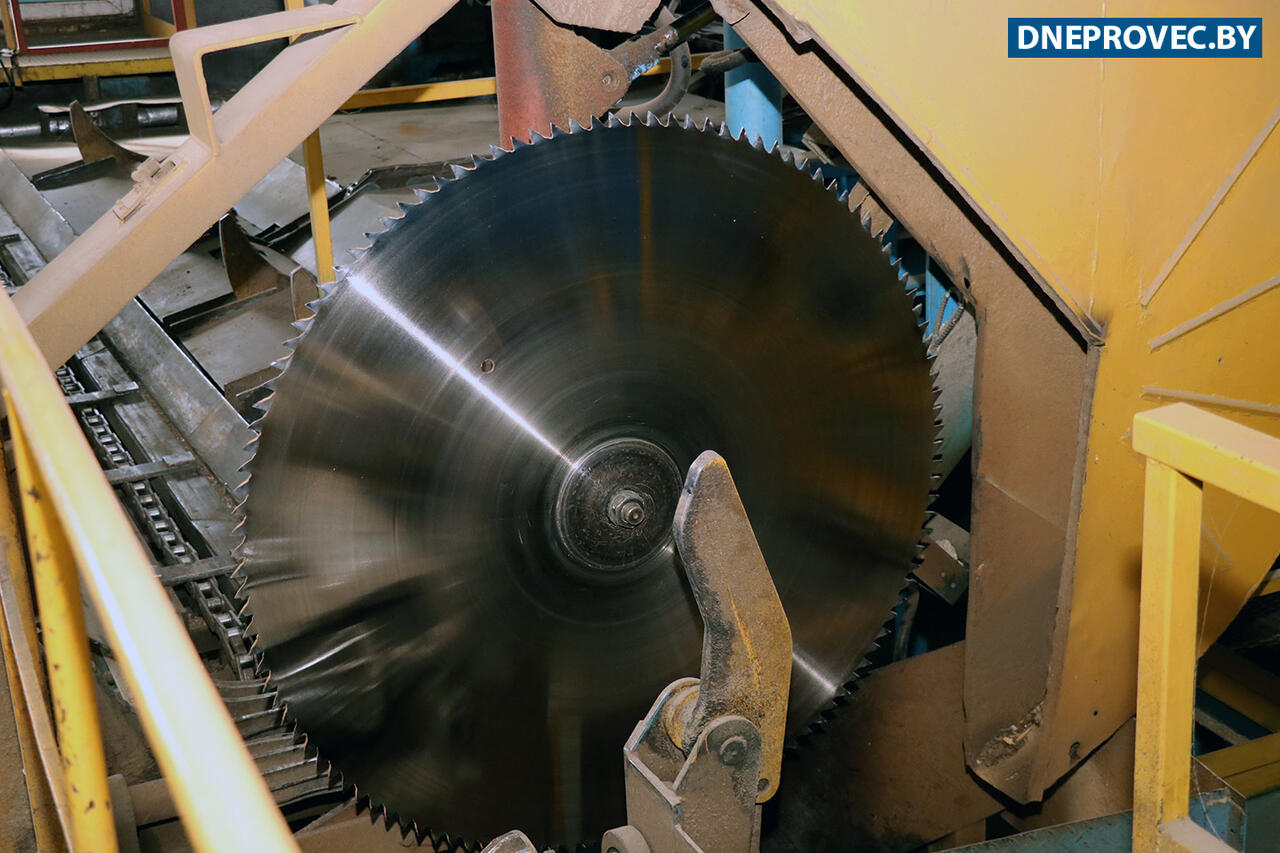
Лущение – это процесс поперечного разрезания древесины, при котором образуется непрерывная линия шпона. Если грубо, то это можно представить себе как чистку картофеля ножом, слой за слоем, при этом «шелуха»-шпон должна получиться максимально длинной и одинаковой толщины – 1,2 миллиметра. Ножи, как и весь необходимый для фанерного производства точный инструмент, точат тут же, в заточном отделении, на итальянском современном оборудовании. Закупить его один раз и обслуживать режущий инструмент на месте гораздо выгоднее, чем отправлять его в стороннюю организацию.
На выходе из станка получается лента шпона шириной 1600 миллиметров, немного меньше, чем длина бревна. Длина ленты с одного бревна на транспортере порой достигает 40 метров! На выходе автоматика отмеряет 1740 миллиметров, и специальный нож рубит ленту на листы, которые складываются в стопки и отправляются на сушку.
3. Сушка и сортировка
Влажность шпона на выходе из линии лущения составляет от 95 до 100%. Сырой шпон поступает в одну из двух автоматизированных линий сушки: Grenzebach (производительность 7 м3/час) и СРГМ 40 (8 м3/час).
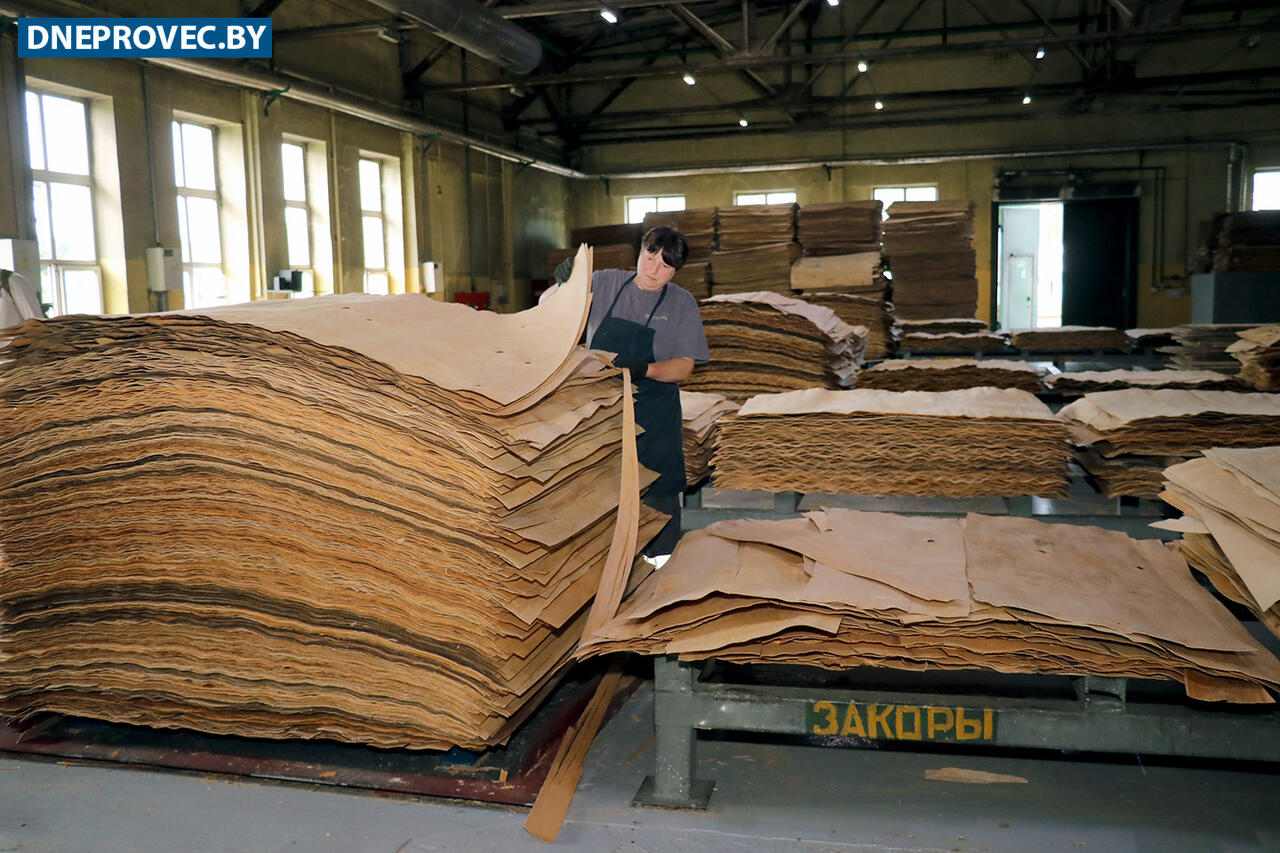
Внутрь сушки шпон закладывается «этажами», которые двигаются внутри линии и обдуваются горячим воздухом. Тепло подается из собственной котельной. Температура – около 180 градусов, она зависит от породы древесины, структуры, толщины шпона. В процессе сушки листы усыхают перпендикулярно древесным волокнам, и в итоге выходит квадрат 1600 на 1600 миллиметров.
Интересный нюанс: когда горячий воздух обдувает древесину, вырабатывается статическое электричество. Работники, которые принимают горячий сухой шпон, конечно, носят средства защиты, но все равно риск получить неприятные ощущения от микроразряда присутствует. Фанерщики разработали небольшое ноу-хау: при помощи арки из медной проволоки и нескольких свободных контактов убирают разряд. Мелочь, а работать намного комфортнее. Банальная физика, школьная программа.
В сортировочном отделении работают люди веселые и вместе с тем выносливые. Тут всегда играет музыка, шумят моторы автопогрузчиков, но много и ручной, трудной работы. Шпон сортируется по сортам. Сортировщик определяет по порокам, небольшим дефектам, однородности рисунка, наличию сучков, к какой категории отнести тот или иной лист. Пойдет ли он на лицевую сторону («рубашку») или будет использован для изготовления упаковки, а может отправиться в стопку с ёмкой надписью «рвань»?
4. Финальные аккорды
Отсортированные листы отправляются в клеевое отделение. Склеивание фанеры производится в горячих гидравлических прессах фирм Kitagava (Япония) и «Волев» (Украина), оснащенных электронной системой управления прессованием, механической загрузкой и выгрузкой. Однако на каждом из работников здесь лежит большая ответственность: именно они формируют пакет для закладки в пресс, выбирают лист того сорта, который нужен. От их компетентности зависит качество конечной продукции. После выдержки листы фанеры обрезаются с четырех сторон на обрезном станке производства ОАО «Пролетарская свобода» (РФ) на размеры, соответствующие требованиям стандартов на продукцию.
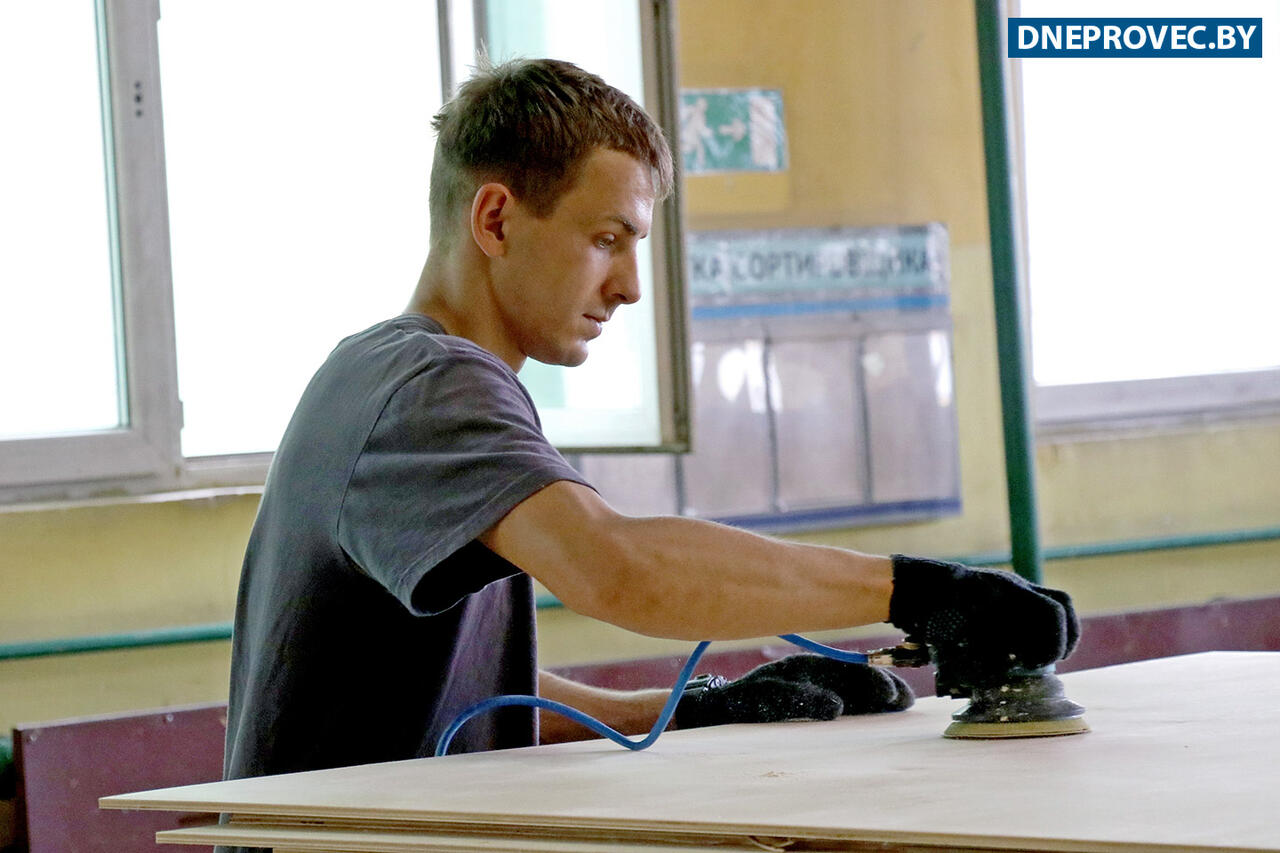
Заключительным этапом процесса производства фанеры является механическая обработка поверхности – шлифование. А дальше – упаковка. Перед упаковкой листы простукиваются, проходят визуальный осмотр, мелкие огрехи и трещинки замазываются специальной шпатлевкой. Фанера готова.
5. Безотходное производство
Фанерное производство уникально еще и потому, что здесь занимаются действительно глубокой переработкой древесины. Помимо основного продукта – фанеры разных сортов – фанерщики выпускают целый ряд попутных товаров.
Так, например, после лущения от бревна остаются «карандаши» – гладкая, обточенная со всех сторон сердцевина диаметром до 80 миллиметров, 1600 миллиметров длиной. Полезная вещь в хозяйстве: можно что-то смастерить или использовать на дрова, породы-то очень подходящие – ольха, береза. Из распиленных по длине «карандашей» получают хоздощечку, которая подходит для декора, заборчиков, внешней отделки. На нее заказов столько, что образовалась целая очередь!
Щепа с остатками клея, обрезки от фанеры идут в котельную – она снабжает теплом сушильные установки. А чистая технологическая щепа, передробленная древесина, отправляется на производство ДСП, там из нее сделают древесно-стружечную плиту. Даже деревянная пыль, которая остается после шлифовки, и та находит свое применение. В специальном аппарате ее прессуют в топливные брикеты, которые прекрасно подходят для печей, котельных, костров и стоят сущие копейки.
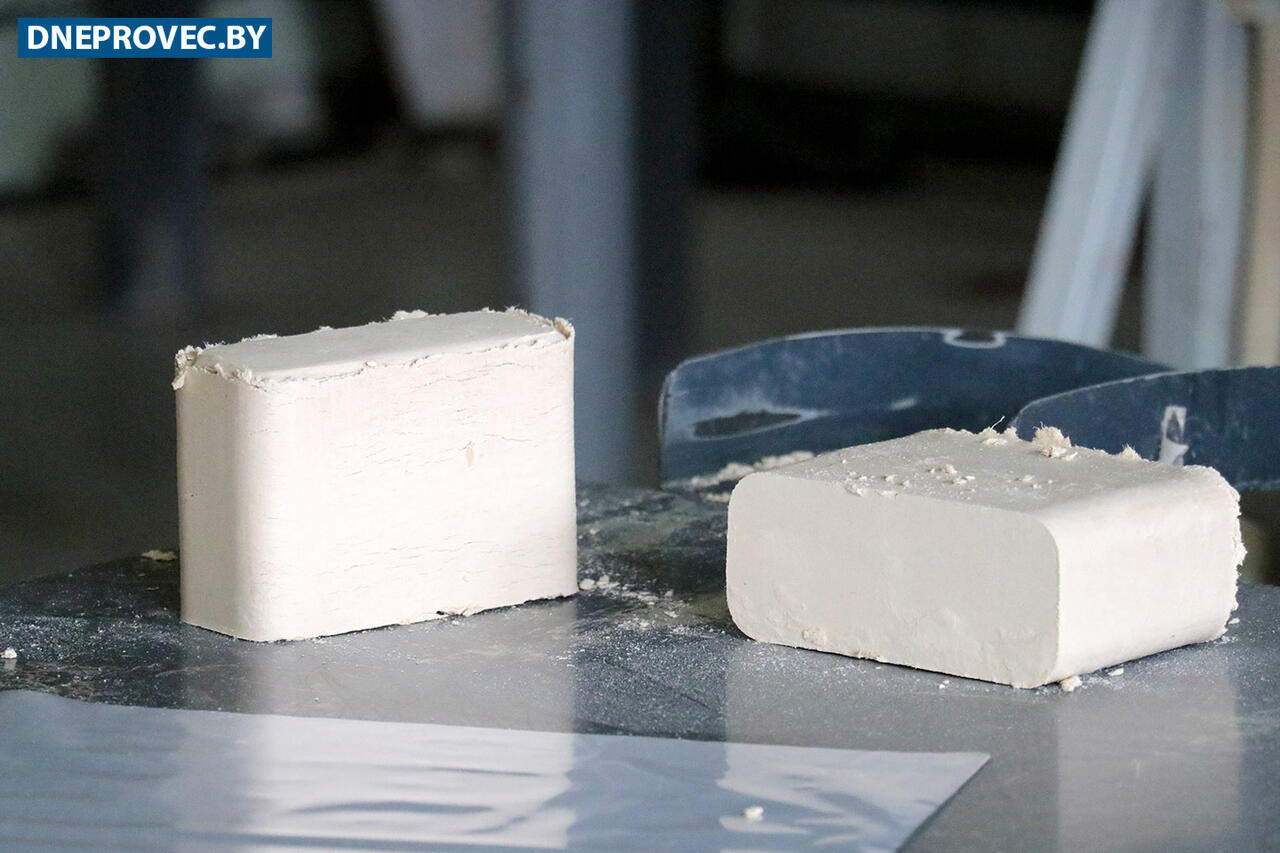