Проект «Как это сделано». Рассказываем о производстве напольного покрытия в ОАО «Гомельдрев»
Источник: Sb.by Фото: Ивана ЯРИВАНОВИЧА
Технология прочности
Создание продукта, которым может гордиться страна, — величайший труд, ответственность и настойчивость, дисциплина и оригинальный подход, стремление превзойти других, а также самих себя. Инициировав учреждение Государственного знака качества, Президент Беларуси возродил славную традицию, заложенную еще во времена СССР, призвав тем самым не только подчеркнуть заслуги людей, вкладывающих в работу душу, но и стимулировать дальнейшие свершения, конкуренцию за право обладать высокой наградой. В конце января Александр Лукашенко вручил первые в истории суверенной Беларуси Государственные знаки качества. Боролись за них сотни товаров, а победителями стали 17, голоса им отдали самые строгие судьи — тысячи белорусских потребителей. «СБ. Беларусь сегодня» начинает мультимедийный проект «Как это сделано», в котором расскажет своим читателям и об отмеченной Знаком качества продукции, и о людях, создающих ее.
Государственного знака качества удостоено напольное ламинированное покрытие VIVAFLOOR ОАО «Гомельдрев». Завод в Речице, где выпускают основу для ламината, с момента запуска заявил о себе как о сверхсовременном производстве и с тех пор ни на йоту не снизил планку. Мы побывали на производственной площадке и узнали, как обеспечивается качество, за которое дают столь высокие награды.
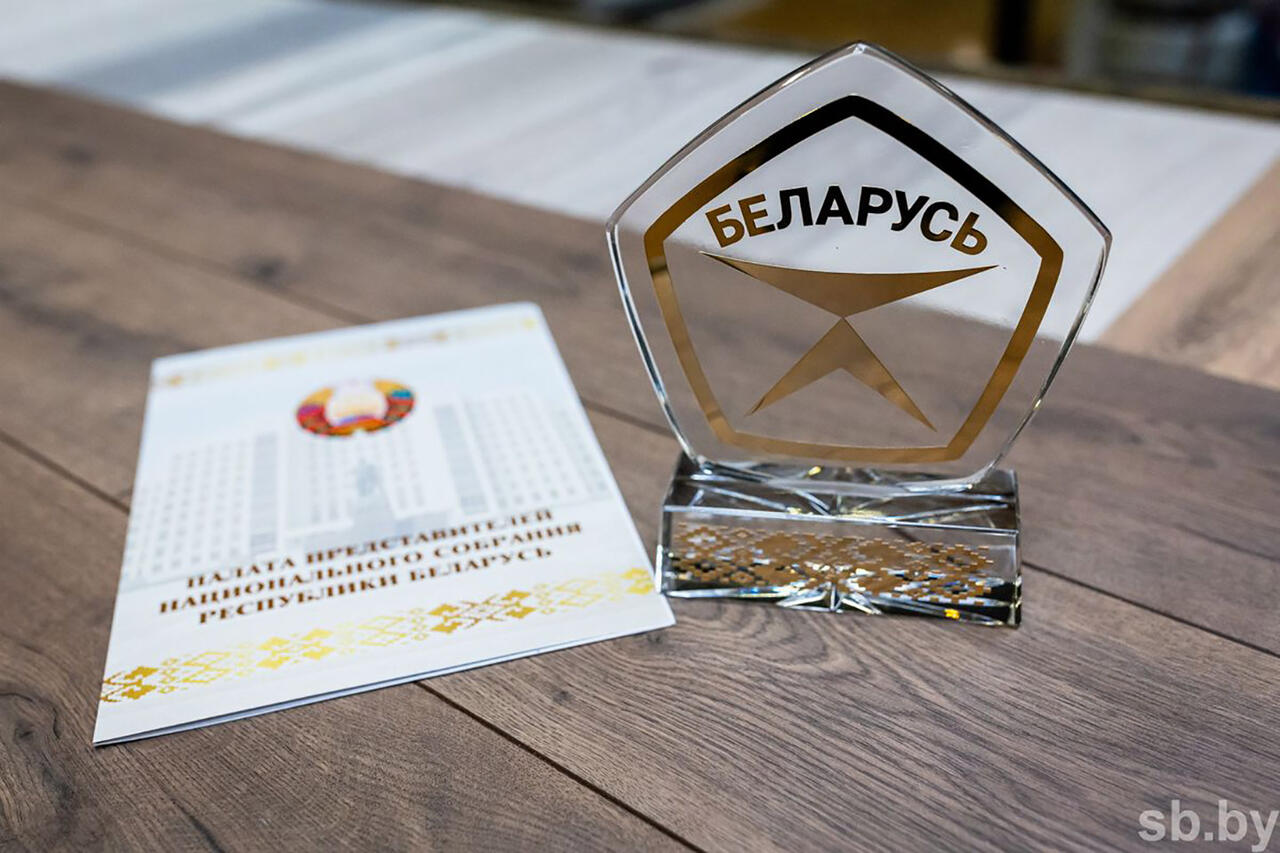
70 процентов сосны и 30 ольхи
Торговый знак VIVAFLOOR запатентован в 2019 году, но первые ламели на заводе по производству плит МДФ в Речице получили еще в 2014‑м. И поскольку емкость белорусского рынка не бесконечна, нужно было сразу разрабатывать пути сотрудничества с другими странами, рассказывает заместитель генерального директора — главный инженер ОАО «Гомельдрев» Юрий Кузнецов и приглашает нас на территорию предприятия:
— Очень тяжело было выйти на внешний рынок: высокая конкуренция. В России, например, приходилось бороться с мировыми брендами. Постепенно убеждая покупателей в высоком качестве продукта, с 2017 года начали работать по его массовому выпуску.
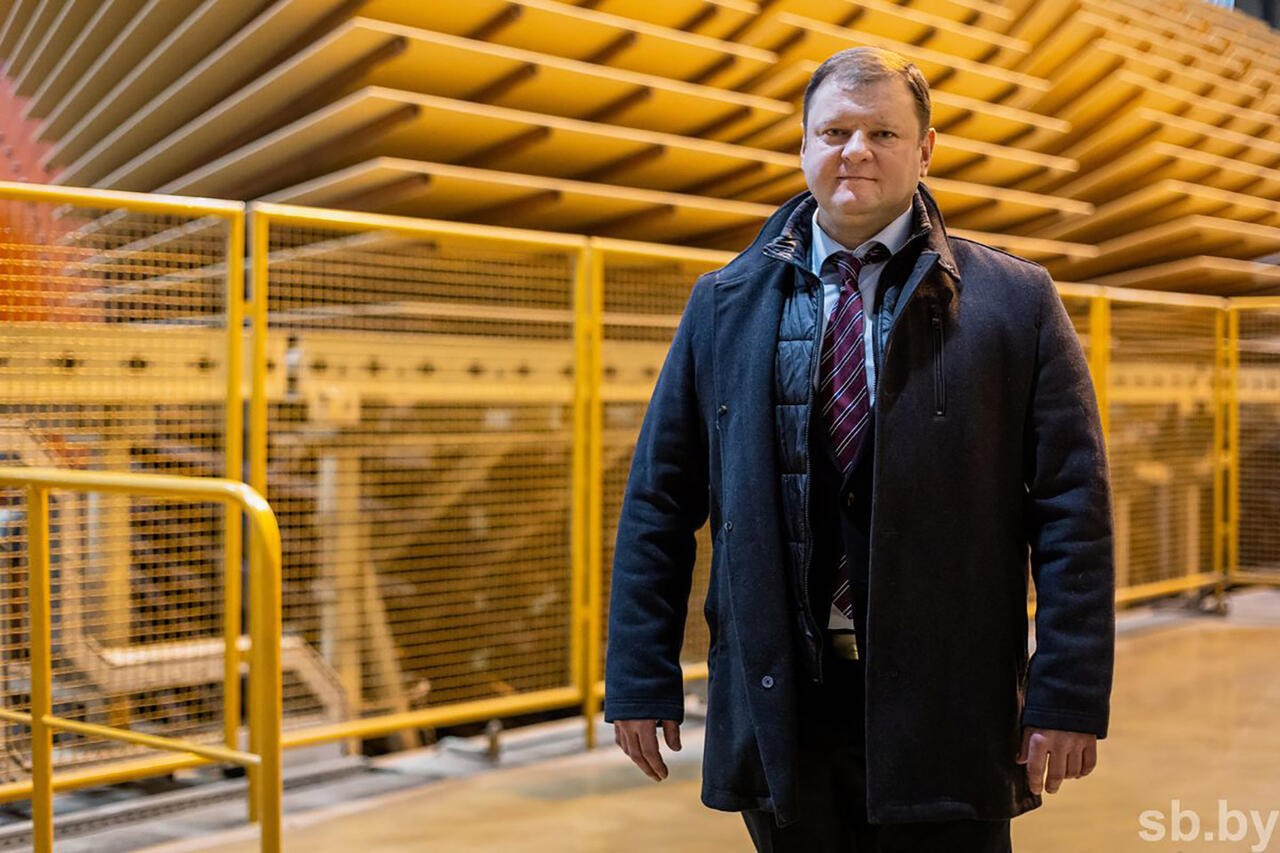
Юрий Александрович предлагает нам проследить производственную цепочку, чтобы понять, из чего складывается надежность напольного покрытия:
— Начинается все с леса, который приезжает на биржу сырья. В основном мы работаем с технологическим сырьем хвойных и лиственных пород — с березой, ольхой, сосной. Частично покупаем, частично заготавливаем в арендном лесном фонде.
Прибывший лес поступает на участок окорки и дробления. Оставшаяся кора не выбрасывается — все идет в дело.
— Здесь мы практически не тратим газ, — объясняет Юрий Кузнецов. — У нас есть несколько модульных блочных газовых котельных, но они используются на станциях водоподготовки и водоочистки, на контрольно‑пропускных пунктах. Во всех остальных случаях сжигаются древесные отходы, кора — и полученную тепловую энергию мы используем в трубе‑сушилке и других технологических процессах.
Окоренный лес поступает в дробилку и превращается в технологическую щепу, которая автоматически распределяется по породам и засыпается в четыре бункера.
— Хвоя, ольха, береза, — на глаз по цвету и плотности определяет породу древесины в бункерах главный инженер.
В зависимости от вида производимой плиты нужен особенный породный состав — это влияет на толщину и плотность изделия. То есть условно в одной плите может быть 70 процентов сосны и 30 ольхи, а в другой — хвойных и лиственных пополам. Условно — потому что точные пропорции производитель не называет. Сохранение коммерческой тайны — одна из составляющих успешной конкуренции на рынке.
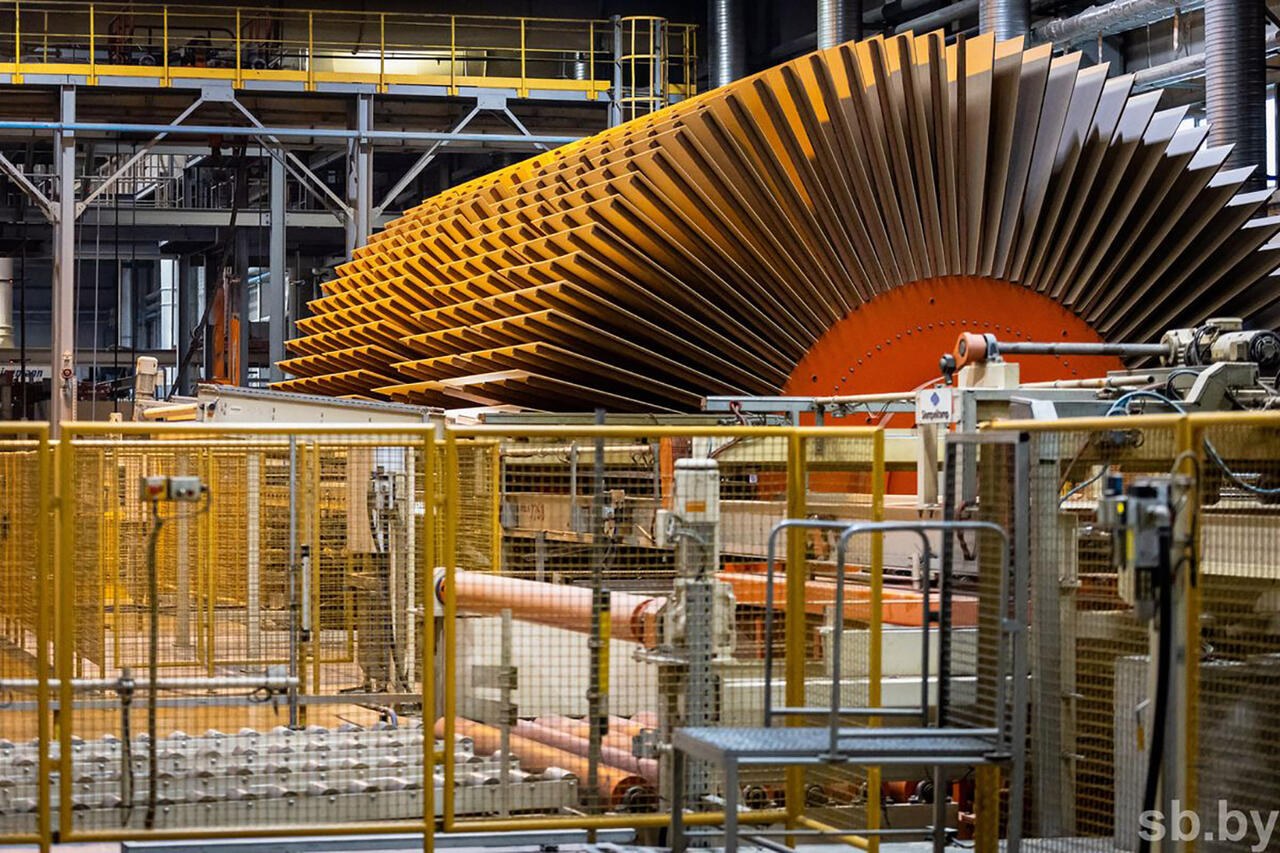
Отдохнуть на «солнышке»
По конвейеру щепа поднимается на сортировку, по пути ее «прощупывает» металлодетектор — никаких лишних деталей в сырье остаться не должно.
— Дальше щепа промывается от песка, пыли и коры. Это позволяет нам уменьшить затраты на дальнейшее производство, бережет оборудование, увеличивая срок его эксплуатации, и повышает качество выпускаемых плит, — объясняет главный инженер.
После мойки щепа под напором воды поступает на участок размола. Сверху она пропаривается и попадает в рафинер, дисковую мельницу, где размалывается в волокно. Волокно пропитывается смолами и всеми необходимыми химическими составами и подается в трубу‑сушилку. Горячий воздух делает его пластичным, а на сепараторе отделяются все не подходящие по плотности элементы.
Юрий Александрович с гордостью демонстрирует нам 37‑метровый пресс. На этой умной линии из вороха волокон в итоге получают прочные и надежные МДФ‑ и ХДФ‑плиты. Механизм сам разрыхляет и выравнивает волокно. По транспортерной ленте «высокий» ковер непрерывно движется от участка к участку, постепенно спрессовываясь и достигая определенной толщины под воздействием давления и температуры, — в прессе она может разниться в зависимости от производственной задачи. Сейчас, например, в разных точках достигает 209 — 214 градусов. Встроенный детектор, как высокоточный УЗИ‑аппарат, по ходу движения проверяет равномерность структуры ковра.
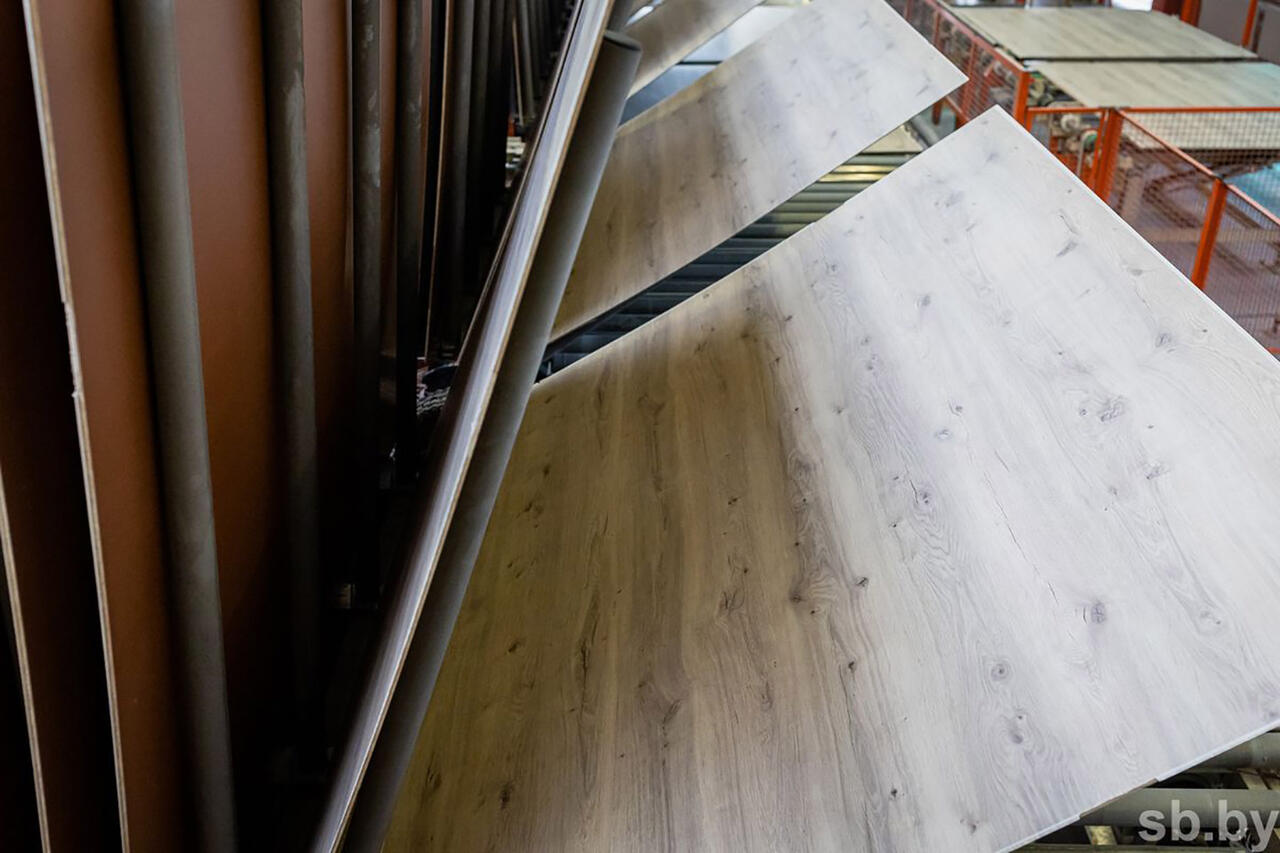
— Технологически мы можем производить плиту толщиной от 3 до 40 миллиметров. На рынке востребованы плиты толщиной от 6 до 38 миллиметров. Кстати, у каждой свое «удостоверение личности». По ходу движения лазер наносит на кромку всю необходимую информацию, включая дату и номер партии.
Плита шлифуется, а в конце пресса стоит участок фрез и диагональных пил — пилят они «наискосок», но, учитывая вектор движения, из плит получаются идеальные прямоугольники. Горячие плиты стабилизируются на веерном охладителе, который на предприятии за живописный вид ласково называют «солнышко». Потом выстаиваются на промежуточном складе. И дальше они готовы к шлифовке. Причем умная машина знает, где именно и сколько «отдыхает» та или иная партия, и забирает ее на линию шлифовки в строго определенный момент.
Гордость за свое дело
Часть идеально ровных плит готова уходить как товарная продукция, часть идет на ламинирование. Варианты последнего для тех или иных готовых изделий разнятся. Обладатель Государственного знака качества — это слоеный «бутерброд», рассказывает начальник участка отделки Геннадий Квасников:
— Ламинируется плита тремя слоями. Внизу подслой — это слой бумаги, который создает прочность и стабильность, делает так, чтобы плиту не выгибало. Сверху наносится декоративный слой, который определяет поверхность полов, уютный и приятный внешний вид. Сейчас у нас на выбор 64 вида декора. Еще один слой — оверлей, меламиновая пленка, пропитанная оксидом алюминия, упрочняющий слой, работающий на истирание. Всю нагрузку от мебели, воды, коготков домашних животных он берет на себя.
На линии ламинирования «бутерброд» запечатывается за 18 — 20 секунд под высоким давлением и воздействием температуры. Она подбирается по ситуации — в зависимости от поставленной задачи и класса изделия.
Завершающая стадия — распил на ламели, за которым пристально следит мастер смены линии ламинированного напольного покрытия Андрей Тартынский:
— Ламинат можно производить с фаской или без нее. В первом случае абсолютно другой вид, более привлекательный. И, кстати, срез покрывается лаками и красками, чтобы не было доступа для воды, поэтому по качеству ни один вид продукции не уступает высоким требованиям.
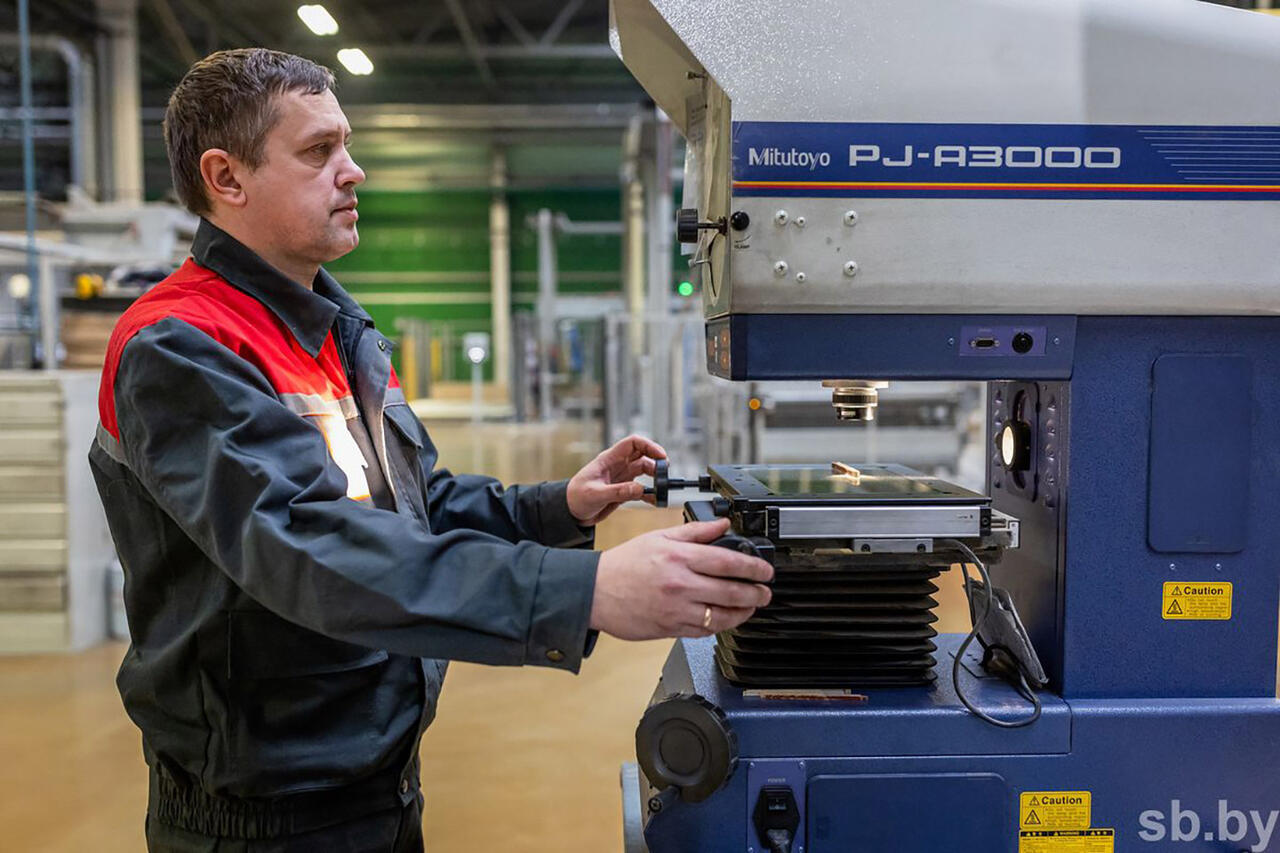
Контролер тут же на месте проверяет все геометрические параметры готового изделия — длину, ширину, толщину, то, как пропилена фаска. Рядом на специальном приборе сверяют, как именно вырезан замок, — ни малейшего расхождения с лекалом быть не должно. Мастер смены подтверждает:
— Качество продукции — наш главный ориентир. Когда Президент Беларуси вручал нашему предприятию Государственный знак качества, гордость испытывали все мои коллеги, ведь каждый из нас приложил руку к созданию продукта. Возродить традицию вручения таких высоких наград было очень правильным решением. Это то, ради чего стоит работать, это благодарность каждому отдельно и всем вместе, что заставляет нас двигаться только вперед.
Завод с нуля
Сегодня ОАО «Гомельдрев» — это четыре производственные площадки. Две находятся в Гомеле, по одной — в Смолевичах и Речице. Завод МДФ в Речице появился после того, как в Ивацевичском районе Брестской области побывал Президент Беларуси и подверг жесткой критике темпы работ по модернизации деревообрабатывающих предприятий республики. Тогда было принято решение о модернизации десяти производств.
Площадка в Речице была выбрана из‑за удачного местоположения. Производство имеет особенности: в сутки приходит тысяча кубометров леса, логистика довольно насыщенная, требующая и автомобильных, и железнодорожных подъездных путей. До развала СССР это была территория действующей военной части и базы хранения ракетного топлива, потому работы по расчистке участка, вывозу леса, демонтажу подземных емкостей были довольно масштабными. В августе 2012 года начался подготовительный процесс, в январе 2015‑го завод ввели в эксплуатацию.
Линии поставили сверхсовременные, учиться работать на них приходилось с нуля. Тогда для Беларуси это производство было настоящим ноу‑хау. В стране не было ни ламинированной МДФ, ни напольных покрытий. Последние и сегодня являются уникальным товаром, только завод МДФ выпускает полы с 4V‑фаской.
Заместитель генерального директора — главный инженер ОАО «Гомельдрев» Юрий Кузнецов подчеркивает:
— Управляющий костяк сегодня — люди, которые строили и запускали завод в те годы, и мы рады, что нам удалось сохранить эту команду, что работники остались верны производству.
Мозговой центр
Завод по выпуску плит МДФ — высокотехнологичное производство, и управляют им специалисты соответствующего уровня. Начальник службы автоматизации и промышленной электроники Юрий Калиниченко знакомит нас с мозговым центром предприятия — пультом оперативного управления. Здесь на огромном количестве мониторов отражена работа всех узлов и механизмов. Только для непосвященного на экранах просто россыпь значков, квадратиков и сокращений. Юрий Калиниченко и его коллеги понимают малейшие хитросплетения схем.
— Каждый «квадратик» или цифра отвечает за свой маленький участок и позволяет нам в режиме реального времени понимать, что происходит: насколько открыты клапаны, как разогревается и держится пресс, каковы уровни заполнения технологических жидкостей и работоспособность форсунок, — рассказывает специалист. — В пультовой все распределено по группам — энергоустановка, клеевая кухня, рафинер, пресс, линия шлифования. За каждую группу отвечает определенный оператор. Здесь работают четыре смены в режиме 24/7 и 365 дней в году. Плановая остановка для ревизии и ремонта предусмотрена только на две недели в году.
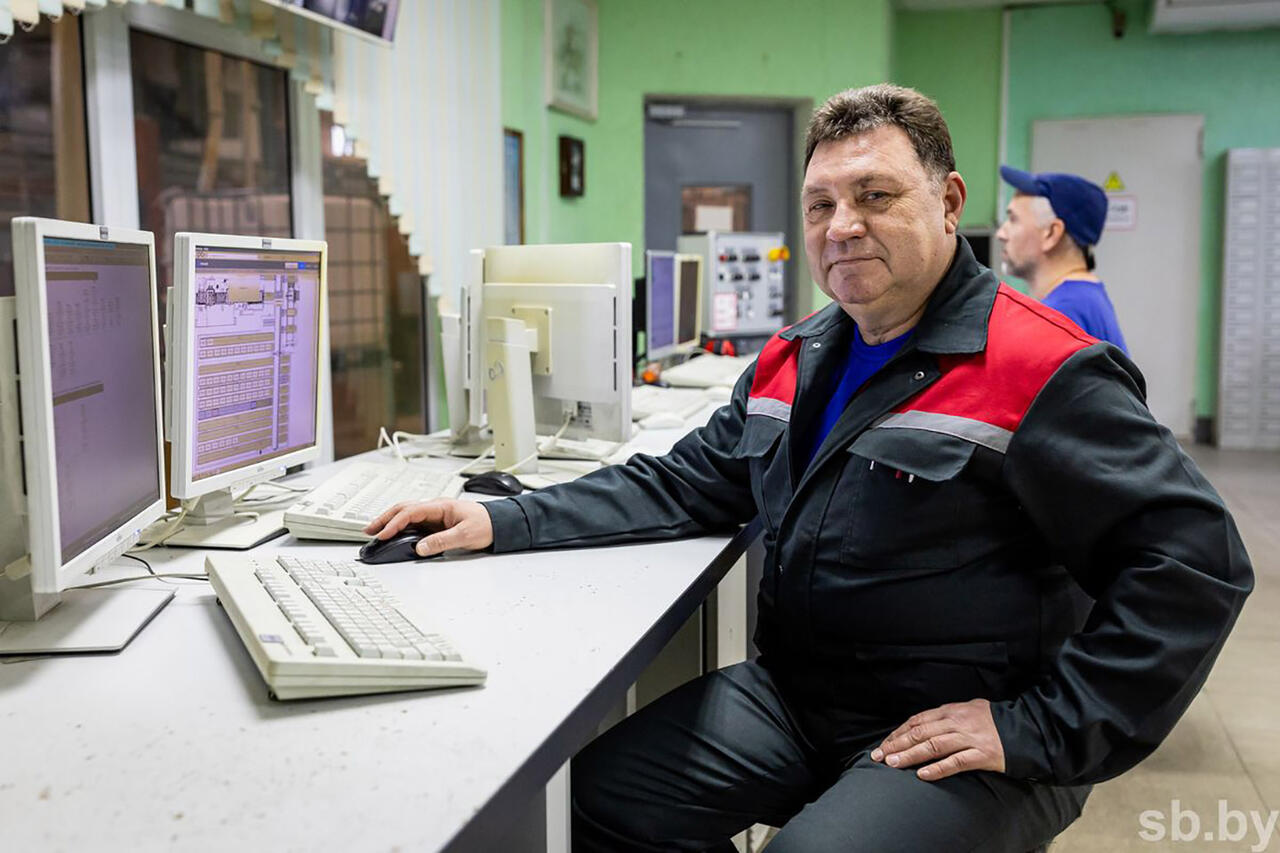
Подразделение Юрия Калиниченко занимается обслуживанием всего завода, всей автоматики и электроники. Инженеры на производстве — сверхграмотные люди, они знают все: от контроллеров и программ, которые в них заложены, до работы всех датчиков, сервоприводов и двигателей, обеспечивающих беспрерывное производство.
Юрий Калиниченко работает здесь с сентября 2014 года — как только начинались первые запуски производства. Сперва было сложно, признается:
— Все новое, неизвестное, но мы не жалели сил на обучение и продолжаем учиться до сих пор. Не бывает такого, что можно остановиться, успокоиться и сказать, что теперь умеешь все. Чем больше мы узнаем, тем больше тонкостей в работе механизмов видим, понимаем и совершенствуем.
Ежедневные испытания
Только по‑настоящему качественная продукция может получить такую высокую оценку, а значит, все этапы ее производства необходимо пристально отслеживать. Качество будущего ламината проверяется на всех стадиях — от прибывающего сырья и ХДФ‑плиты, которая идет в основу ламинированных напольных покрытий, до декоративной пленки и готового изделия. Причем все моменты строго регламентированы, рассказывает начальник службы технического контроля управления качества Наталья Захожая:
— Проверяют самые разные позиции согласно техрегламентам, которые разработаны в соответствии с качественными показателями СТБ 13329 — 2018. Мы в очередной раз получили сертификат соответствия этому стандарту и стараемся держать марку. Есть у нас сертификат пожарной безопасности России. Ежегодно ламинат сдается в независимую лабораторию для проверки соответствия СТБ и проходит испытания на санитарно‑гигиеническую безопасность для населения.
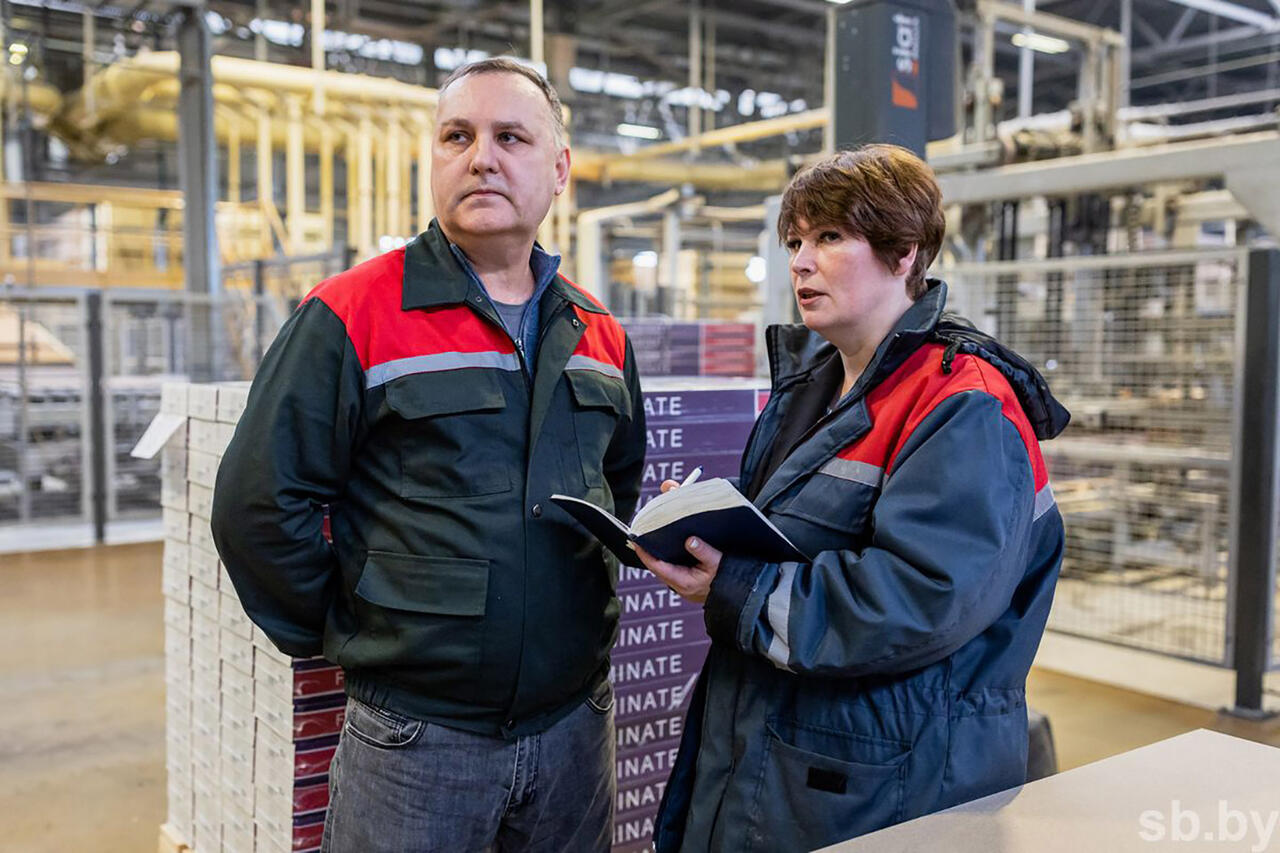
Дышать химией потребитель не будет. На содержание формальдегида проверяется не только плита, но и все поставленное сырье и материалы.
Ежедневно ламели поступают на физико‑механические испытания. Боитесь проливать воду на ламинат? Завод МДФ свою продукцию тестирует и на разбухание. Небольшой прямоугольный элемент продукции замачивается на 24 часа в 20‑градусной воде, а через сутки обсушивается и измеряется. Разбухнуть после такой продолжительной ванны он может максимум на 15 — 18 процентов, в зависимости от класса. Но на практике ни один из образцов максимальных пределов разбухания не достигал. И, кстати, по технологии замок на ламели запечатывается воском, чтобы вода не попала даже в малейшие щели.
На ламинат здесь бросают металлические шарики, елозят по нему роликами компьютерных кресел, а еще и каждый день сгибают, «рвут» и ломают. Лаборант химического анализа производственной лаборатории Галина Коцур демонстрирует все на практике:
— Каждые три часа в лабораторию поступает произведенная плита, где проверяют ее предел прочности на изгиб, растяжение, отрыв. Вот у нас специальная разрывная машина, где держателями фиксируют образец и подвергают его самым разным испытаниям. А в соседнем агрегате мы при помощи рентгена проверяем плотность продукта.
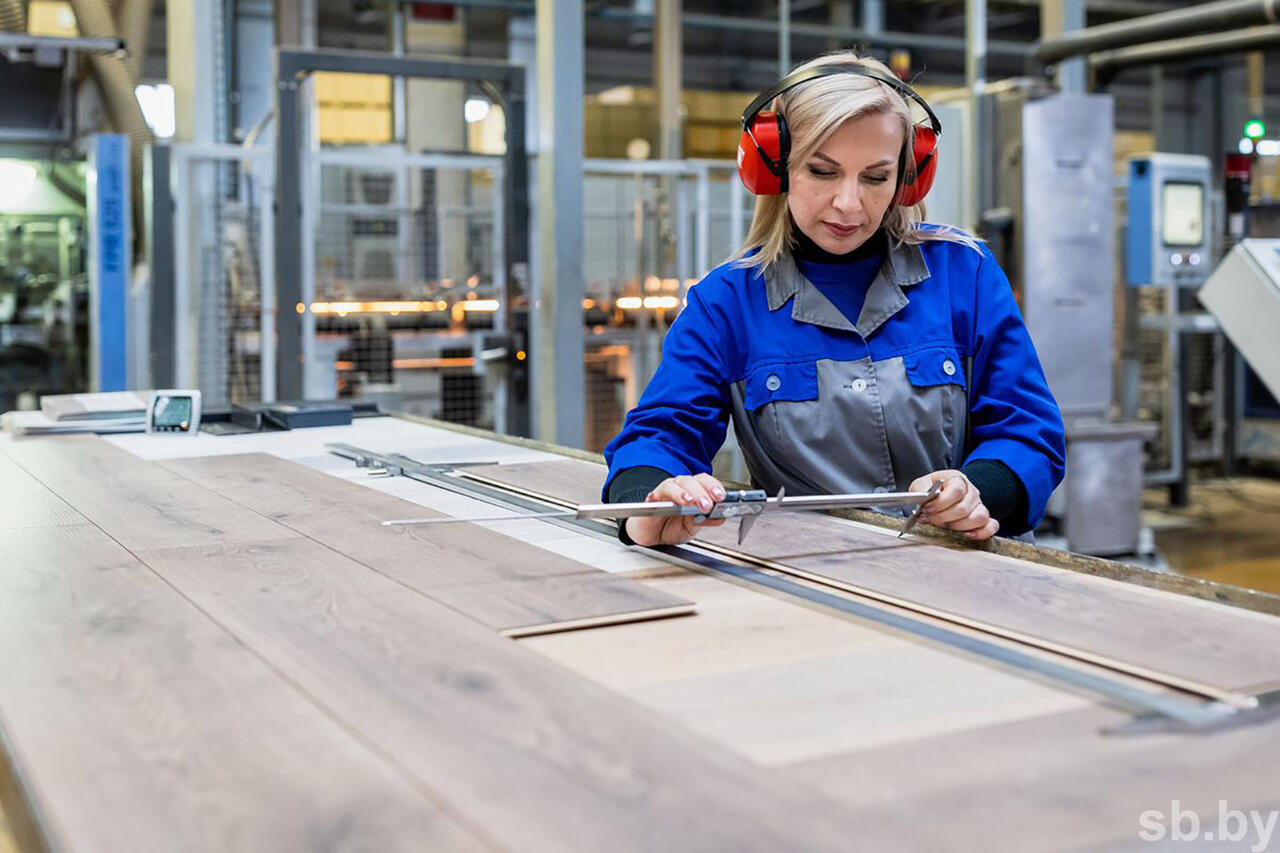
В дальнейшем предполагается расширить линейку продукта. Руку всегда нужно держать на пульсе — выводить из производства декоры, которые не пользуются спросом, замещать их более актуальными видами. Речицкий завод в настоящее время производит напольные покрытия толщиной 8 миллиметров. В следующем месяце возьмутся за эксперимент — запустят производство 10‑миллиметровых плит, структура у них более мощная. На рынке есть ниша для такого товара, клиенты давно просят — кому‑то удобнее работать с 10‑миллиметровым изделием.
Хороший спрос на покрытие VIVAFLOOR и за рубежом. Основные направления экспорта — Россия, Казахстан, Азербайджан, Узбекистан, небольшие партии отправляются в Монголию. Ведутся переговоры с дилерскими сетями о поставках в Иран и Сирию.
Если говорить в целом о планах ОАО «Гомельдрев» — там намерены повышать процент загрузки имеющегося оборудования, увеличивая сменность и расширяя ассортимент. Конечно, прорабатываются идеи о внедрении новых и перспективных видов продукции, но эти планы на предприятии пока суеверно хранят в тайне.
ПРЯМАЯ РЕЧЬ
Генеральный директор ОАО «Гомельдрев» Максим Соляник:
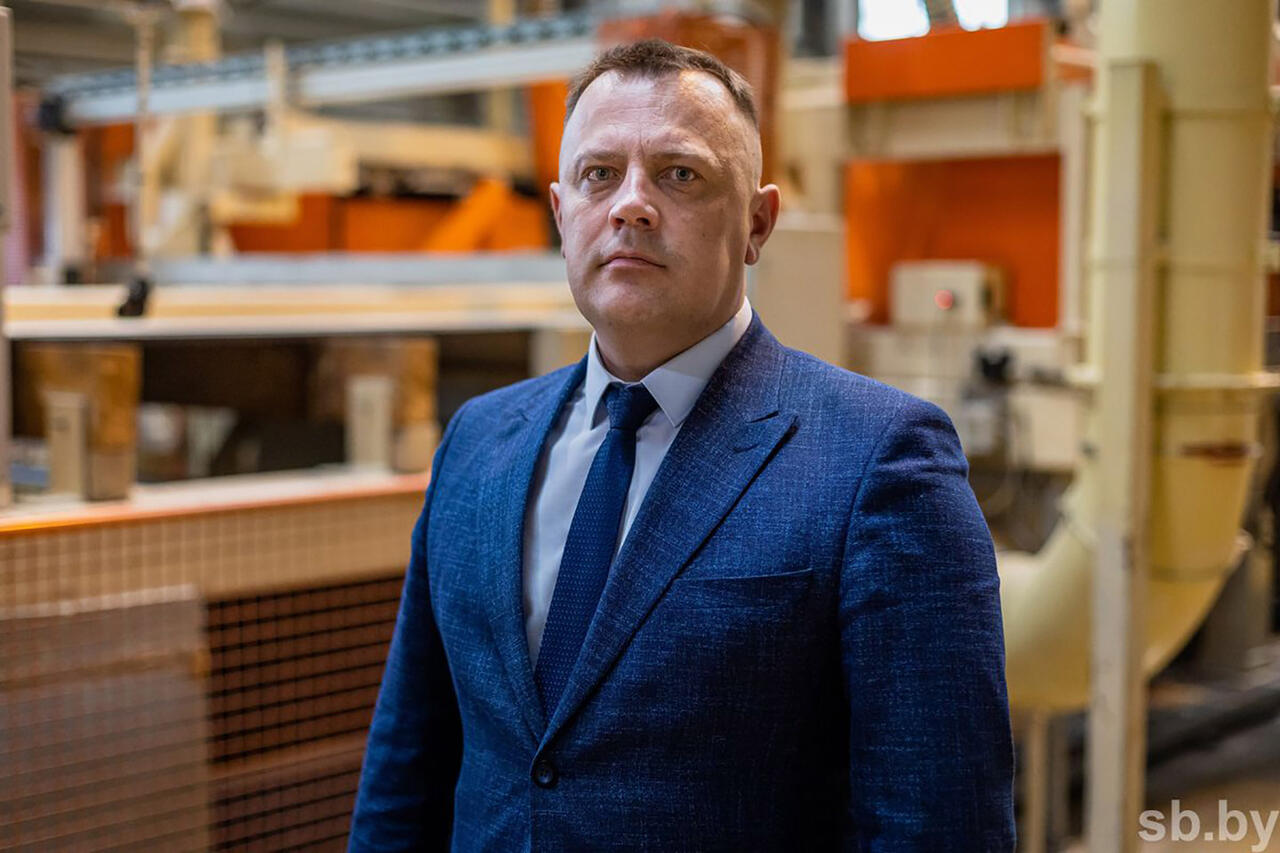
— Присвоение Государственного знака качества — огромный прорыв для предприятия с коммерческой точки зрения. Знак качества — символ доверия к производству, что влечет лояльность клиентов и увеличение продаж. Но самое главное — высокая ответственность. Теперь мы ни на полшага не можем отступить назад, не можем позволить себе сложить руки и почивать на лаврах — мы должны приумножать и развивать свои достижения.
Напольное ламинированное покрытие VIVAFLOOR — итог глубокой переработки исходных материалов с наиболее высокой добавленной стоимостью. Знак качества получила продукция, создаваемая руками всего коллектива, а это 1900 человек. Поэтому это наша общая победа и общая гордость за то, что производим качественный белорусский продукт.
valchenko@sb.by
Полная перепечатка текста и фотографий запрещена. Частичное цитирование разрешено при наличии гиперссылки на оригинал статьи.